DARPA's new missile hints at truly game-changing technology - Sandboxx
Last week, the Defense Advanced Research Projects Agency (DARPA) quietly unveiled a new high-speed missile program called Gambit. The program is meant to leverage a novel method of propulsion that could have far-reaching implications not just in terms of weapons development, but for high-speed aircraft and even in how the Navy’s warships are powered.
The Defense Advanced Research Projects Agency will host an industry event on Aug. 16 in Arlington, Virginia, to discuss a forthcoming program that centers around propulsion technology envisioned to power a long-range air-to-ground strike weapon system.
DARPA expects the two-phase Gambit project to last 36 months with the goal of developing and demonstrating a rotating detonation engine, according to a notice posted Monday on SAM.gov.
The first phase will cover preliminary RDE design work and direct-connect combustor and freejet inlet tests, followed by detailed system design and tip-to-tail testing in simulated flight environments.
Efforts under the program seek to pave the way for a flight test of a high-supersonic weapon prototype, DARPA noted.
Interested business representatives should register in advance to attend the proposers’ day as the agency will fill accept registrations on a first-come, first-served basis.
This propulsion system, known as a rotation detonation engine (RDE), has the potential to be lighter than existing jet engines while offering a significant boost in power output, range, and fuel efficiency.
The Gambit missile is just one of a number of programs placing a renewed focus on RDE technology, though for the most part, these systems have managed to fly under the media’s radar. That is, except for Aviation Week & Space Technology Defense Editor Steve Trimble, who has covered these recent developments at length. Trimble was kind enough to discuss that work with me as I sought to better understand just how big a deal this technology could be.
Rotation Detonation Engines may not be common in discussion today, but amid the ongoing hypersonic arms race and America’s renewed focus on deterring near-peers, this technology could help offset a number of tactical and strategic advantages presented by America’s opponents in places like Europe and the Pacific…
…And it may be closer than you think.
Related: Is America really losing the hypersonic arms race?
A new kind of propulsion system
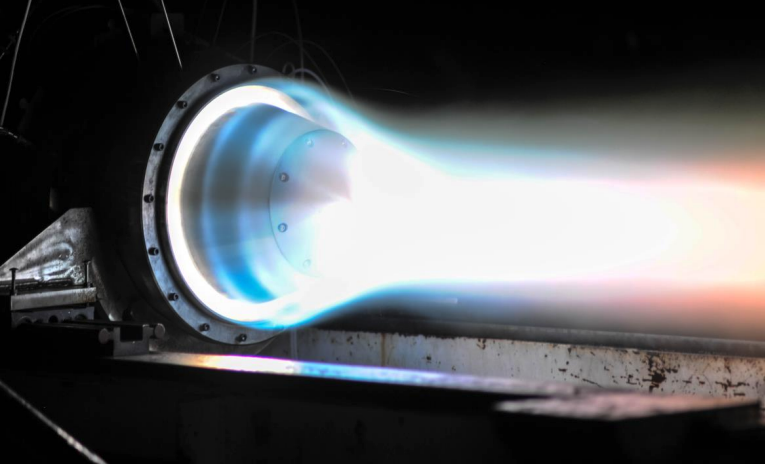
Rotating detonation engines have been the subject of theory and speculation for decades, but have yet to cross the barrier between theory and practical application.
In theory, a rotating detonation engine promises to be much more efficient than traditional jet engines, potentially providing missile applications a serious boost in range and speed. That could also mean fielding smaller weapons capable of achieving the same speeds and ranges as today’s missiles.
In aircraft applications like jet fighters, rotation detonation engines could offer similar benefits to missiles in terms of range and speed, while potentially reducing maintenance requirements. Fighters, in particular, rely on afterburners, which effectively firehose fuel into the engine’s exhaust stream for added thrust, which, you can imagine, rapidly depletes fuel stores and reduces the fighter’s range. RDEs could potentially allow for a similar boost in thrust with a dramatically reduced fuel penalty.
But where this technology could be the most useful is in powering the Navy’s future non-nuclear surface vessels, providing increased power production, range, and speed while having a seriously beneficial impact on the Navy’s budgetary bottom line.
Related: The Air Force is eyeing groundbreaking new engines for the F-35
Harnessing the power of detonation
The concept behind rotation detonation engines dates back to the 1950s. In the United States, Arthur Nicholls, a professor emeritus of aerospace engineering at the University of Michigan, was among the first to attempt to develop a working RDE design.
In some ways, a Rotating Detonation Engine is an extension of the concept behind pulse detonation engines (PDEs), which are, in themselves, an extension of pulsejets. That might seem confusing (and maybe it is), but we’ll break it down.
Pulsejet engines work by mixing air and fuel within a combustion chamber and then igniting the mixture to fire out of a nozzle in rapid pulses, rather than under consistent combustion like you might find in other jet engines.
In pulsejet engines, as in nearly all combustion engines, igniting and burning the air/fuel mixture is called deflagration, which basically means heating a substance until it burns away rapidly, but at subsonic speeds.
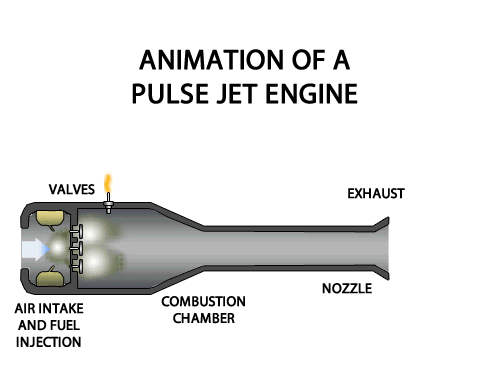
A pulse detonation engine works similarly, but instead of leveraging deflagration, it uses detonation. At a fundamental level, detonation is a lot like it sounds: an explosion.
While deflagration speaks to the ignition and subsonic burning of the air/fuel mixture, detonation is supersonic. When the air and fuel are mixed in a pulse detonation engine, they’re ignited, creating deflagration like in any other combustion engine. However, within the longer exhaust tube, a powerful pressure wave compresses the unburnt fuel ahead of the ignition, heating it above ignition temperature in what is known as the deflagration-to-detonation transition (DDT). In other words, rather than burning through the fuel rapidly, it detonates, producing more thrust from the same amount of fuel; an explosion, rather than a rapid burn.
“The detonation process is a more rapid and efficient extraction of energy from your fuel from a thermodynamic standpoint when compared to deflagration,” Dee Howard endowed professor of hypersonic and aerospace engineering, Dr. Chris Combs, told Sandboxx News.
The detonations still occur in pulses, like in a pulsejet, but a pulse detonation engine is capable of propelling a vehicle to higher speeds, believed to be around Mach 5. Because detonation releases more energy than deflagration, detonation engines are more efficient — producing more thrust with less fuel, allowing for lighter loads and greater ranges.
The detonation shockwave travels significantly faster than the deflagration wave leveraged by today’s jet engines, Trimble explained: up to 2,000 meters per second (4,475 miles per hour) compared to 10 meters per second from deflagration.
In May of 2008, the Air Force Research Laboratory made history by building the world’s first crewed pulse detonation-powered aircraft, using a Scaled Composites home-build plane called the Long-EZ. The unusual franken-plane managed a speed higher than 120 miles per hour during its test flight, with test pilot Pete Siebold at the stick, and reached altitudes between 60 and 100 feet.
“This is a potential game-changer in terms of fuel efficiency,” The AFRL’s Propulsion Directorate’s Fred Schauer said of the PDE powering Long-EZ.
“For comparison, if we had operated this same engine with conventional combustion we would have made less than a third of the thrust for the same fuel burn. In comparison to traditional engines, fuel savings of 5 to 20 percent could be expected.”
The Air Force assessed at the time that improvements to their PDE engine could eventually propel aircraft to speeds beyond Mach 4, and higher if combined with other advanced propulsion systems like scramjets. A rotation detonation engine could be even more effective, but many within the academic and engineering communities questioned whether such an engine could ever actually be built.
Related: US announces successful tests of 3 hypersonic missiles in 2 weeks
The Rotation Detonation Engine emerges
A rotating detonation engine takes this concept to the next level. Rather than having the detonation wave travel out the back of the aircraft as propulsion, it travels around a circular channel within the engine itself.
Fuel and oxidizers are added to the channel through small holes, which are then struck and ignited by the rapidly circling detonation wave. The result is an engine that produces continuous thrust, rather than thrust in pulses, while still offering the improved efficiency of a detonation engine. Many rotation detonation engines have more than one detonation wave circling the chamber at the same time.
As Trimble explains, RDEs see pressure increase during detonation, whereas traditional jet engines see a total pressure loss during combustion, offering greater efficiency. In fact, rotation detonation engines are even more efficient than pulse detonation engines, which need the combustion chamber to be purged and refilled for each pulse.
“In theory, RDE is a bit like the leap from turbojets to turbofans in the 1960s, but for high-supersonic vehicles. It should give you a big jump in specific impulse (aka fuel efficiency), and if you can figure out how to package it in a way that doesn’t make things significantly heavier or less aerodynamic, you should be able to get a nice range boost out of it,” Trimble explained.
In 2020, a team out of the University of Central Florida, working with the Rotating Detonation Rocket Engine Program at the Air Force Research Laboratory, successfully built and tested the world’s first working rotation detonation engine that continued firing until its fuel was cut off, effectively proving the concept was possible. The three-inch copper test rig developed by the team successfully produced 200 pounds of thrust in laboratory conditions.
Since then, a number of other programs have followed suit, with noted engine manufacturer Pratt and Whitney among those leading the charge.
Related: How America almost got hypersonic aircraft decades ago
A new generation of high-speed, long-range weapons
On July 18, DARPA released a Special Notice pertaining to their new Gambit Missile program, announcing a “Proposer’s Day” for firms to get more information about the effort and its aims. Within the notice, DARPA included a description of the program and its objectives, as well as their anticipated timeline, from inception to flight test.
“The objective of the Gambit program is to develop and demonstrate a novel Rotating Detonation Engine (RDE) propulsion system that enables a mass-producible, low-cost, high-supersonic, long-range weapon for air-to-ground strike in an anti-access/area denial (A2AD) environment.”
The program will be conducted in two 18-month phases. The first will entail competitors completing their preliminary designs with some limited testing, while the second would finalize designs and culminate in full-scale flight tests of an RDE system.
While the release offers scant details on the overarching goals of Gambit, some of the language within the announcement point toward specific challenges America’s defense apparatus currently finds itself facing. The reference to Gambit’s use in an “anti-access/area denial (A2AD) environment” could pertain to anywhere American forces are squaring off against a near-peer adversary. But there’s one such environment that has been the focus of multiple Defense efforts in recent years: the 1,000-mile-plus area denial bubble extending from Chinese shores thanks to a growing array of anti-ship weapon systems.
America’s carrier-based fighters, the F-35C and F/A-18 Super Hornet, each have a combat radius of less than 650 miles, which would mean having to sail carriers into harm’s way to launch combat sorties without longer-range munitions.
The United States obviously has the capability of fielding air-launched missiles with significant range, but it isn’t as simple as mounting a massive rocket under the Super Hornet’s wing, as Trimble points out. The size of these weapons matters a great deal, which is why RDE engines, with their improved efficiency and smaller mass, could be a game changer.
“That is probably most useful for the US Navy, which needs to find a way to equip fighters with long-range, high-speed (Mach 4-6) cruise missiles that are small enough to squeeze onto an aircraft carrier’s weapons elevators and land back on the carrier under a fighter’s wing without slamming into the deck.”
But Gambit isn’t the first new weapon program to leverage rotation detonation engine technology. According to the Air Force Research Lab, RDE technology could make high-speed weapons much more affordable, which is of particular import following a recent Defense Department analysis that indicated the hypersonic (Mach 5+) weapons in development for the Air Force may cost as much as $106 million each.
According to a list of efforts supported by the Pentagon’s High-Performance Computing Modernization program in 2022, the Air Force Research Lab has begun development on at least three RDE weapons or demonstrators.
One aims to field a liquid-fueled rotating detonation scramjet that will power an air-to-surface missile that can be carried internally by 5th generation fighters. Another will leverage solid fuel for an air-to-air missile, and a third effort aims to develop a vehicle for freejet testing on the ground.
RDE technology could eventually also lead to smaller weapons that offer the same range and speed as today’s missiles, allowing stealth aircraft like the F-35 to carry more munitions inside their internal weapons bays. Likewise, missiles of the same size as today’s could fly further faster, which has far-reaching benefits in both air-to-air and air-to-surface operations.
Related: Why calling Russia’s Kinzhal a ‘hypersonic missile’ is a stretch
Rotation Detonation Engines could power fighters and even the Navy’s warships
Among the weapon-oriented programs being developed by the Air Force Research Laboratory is another rotation detonation engine enterprise that could offer America’s fighters a big boost in range and speed: an RDE that could be used in place of a fighter’s afterburner.
An afterburner effectively combines the remaining oxygen leaving the jet engine with more fuel by spraying fuel directly into the outflow of exhaust. Needless to say, this method of increasing thrust takes a heavy toll on the aircraft’s fuel stores, forcing pilots to choose between speed and range or loiter time.
A rotation detonation engine afterburner could provide an increase in thrust while leveraging the design’s inherent efficiency, providing the same gains for less fuel expended.
In the longer term, air-breathing RDEs could even find their way into the fuselage of an aircraft as the primary means of propulsion. But not all of the potential applications for RDE’s are in the sky. One of the most promising may actually be out at sea.
While the Navy’s aircraft carriers and submarines are famously nuclear-powered, the rest of the fleet still runs on good old-fashioned F-76 marine diesel fuel — an estimated 86 million barrels of it in 2016 alone. So it may come as little surprise to you that the Navy has been very interested in this approach to high-efficiency propulsion. In fact, the Navy filed its own patent for a “rotary detonation engine” as far back as 1982.
According to the Navy in 2012, rotation detonation engines could increase a warship’s thrust by 10% and reduce fuel consumption by 25%, giving them more speed and range for the fuel expended. In 2012, that kind of improvement was projected to result in savings of $300 to $400 million per year, which equates to $387 million to $516 million in today’s dollars.
The truth is, Rotation Detonation Engines could help fighters fly further, missiles fly faster, ships sail longer, and even rocket launches become cheaper. There aren’t many places in America’s defense apparatus this forward-reaching tech couldn’t benefit.
And while for many years the question surrounding RDEs was always if, increasingly, it now appears to be when.
Read more from Sandboxx News
- What kind of fighter could the latest military tech really build?
- Navy still pouring millions into shipboard laser weapon development
- Why does the media report on secretive defense programs? Should this tech be classified?
- Hypersonic weapons could rescue the Navy’s stealth destroyer
- Is the famous TB2 Bayraktar the best drone in Ukraine?
Rotating Detonation Engines
Rotating detonation engines (RDEs) are a promising technology for future propulsion and energy systems due to their high potential thermodynamic efficiencies and compact designs.
However, the development of these devices into robust, reliable systems requires continued experimentation. In the Hanson Research Group, we work with engine experts at the Naval Postgraduate School to support these experimentation efforts by developing laser sensors to measure H2O, CO2, CO, and temperature within their RDE combustors. The unique geometry of rotating detonation engine combustors led us to pioneer a single-ended sensor design, wherein laser light is both delivered and collected through the same window on the engine.
In combination with advanced diagnostic techniques that are able to overcome the intense vibration and thermal emission generated by the engine, our single-ended sensors provide crucial combustion data that will inform future rotating detonation engine designs.
To learn more, check out some of our publications:
[1] Peng, W. Y., Goldenstein, C. S., Spearrin, R. M., Jeffries, J. B., Hanson, R. K., “Single-ended mid-infrared laser-absorption sensor for simultaneous in situ measurements of H2O, CO2, CO, and temperature in combustion flows,”
Applied Optics, Vol. 55, No. 33 (2016) pp. 9347–9359. DOI: 10.1364/ao.55.009347
[2] Peng, W. Y., Cassady, S. J., Strand, C. L., Goldenstein, C. S., Spearrin, R. M., Brophy, C. M., Jeffries, J. B., Hanson, R. K., “Single-ended mid-infrared laser-absorption sensor for time-resolved measurements of water concentration and temperature within the annulus of a rotating detonation engine,”
Proceedings of the Combustion Institute, Vol. 37, No. 2 (2019) pp. 1435–1443. DOI: 10.1016/j.proci.2018.05.021
[3] Cassady, S. J., Peng, W. Y., Strand, C. L., Dausen, D. F., Codoni, J. R., Brophy, C. M., Hanson, R. K., “Time-resolved, single-ended laser absorption thermometry and speciation in a H2/C2H4-fueled rotating detonation engine,”
Proceedings of the Combustion Institute, Vol. 38, No. 1 (2021) pp. 1719–1727. DOI: 10.1016/j.proci.2020.06.125
[4] Peng, W. Y., “Single-ended laser-based diagnostics for thermometry and speciation in detonation-driven combustors,”
Ph.D. Thesis, Stanford University (2019)
A Florida team working with the US Air Force claims that it's built and tested an experimental model of a rotating detonation rocket engine, which uses spinning explosions inside a ring channel to create super-efficient thrust.
The vast majority of engines, of course, use combustion rather than detonation to achieve their output goals. Combustion is a relatively slow and controlled process resulting from the reaction between fuel and oxygen at high temperatures, and it's very well understood and mature as a technology.
Detonation, on the other hand, is fast and chaotic and much less predictable. An explosion instead of a burn, it is the massive discharge of energy you get when you break apart the chemical bonds holding an explosive molecule together by giving it a jolt of energy – either electrical or kinetic – in the form of a sufficiently powerful shockwave to destabilize those bonds. Detonation is excellent when you want to wreck stuff in bulk, and much harder to maintain precise control over.
But when you need to break the chains of the Earth's gravity and go to space, every gram of weight makes things that much harder and more expensive. Detonation releases significantly more energy from significantly less fuel mass than combustion, so for more than 60 years, rocket scientists have been working on the idea of a rotating detonation rocket as a potential way to cut down weight and add thrust.
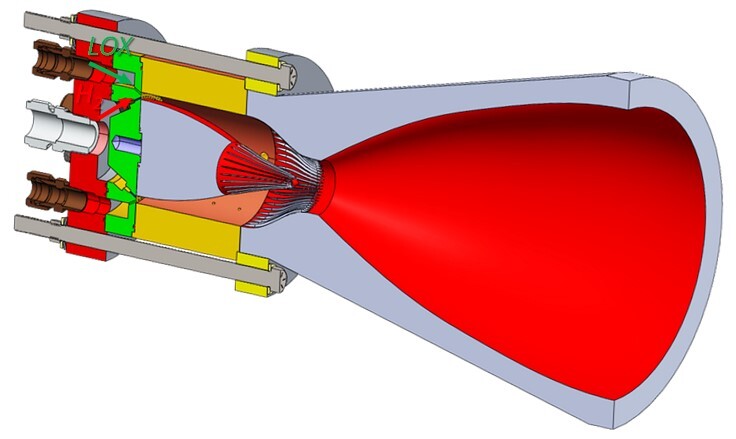
Professor Kareem Ahmed, University of Central Florida
In essence, such a device starts with one cylinder inside another larger one, with a gap between them and some small holes or slits through which a detonation fuel mix can be pushed. Some form of ignition creates a detonation in that annular gap, which creates gases that are pushed out one end of the ring-shaped channel to produce thrust in the opposite direction. But it also creates a shockwave that propagates around the channel at around five times the speed of sound, and that shockwave can be used to ignite more detonations in a self-sustaining, rotating pattern if fuel is added in the right spots at the right times.
Pioneered by engineers at the University of Michigan in the 1950s, the rotating detonation engine is tantalizingly simple in a mechanical sense, but this self-propagating detonation wave has proven torturously difficult to achieve and sustain.
Until now, it seems. A team at the University of Central Florida, working alongside the Rotating Detonation Rocket Engine Program at the Air Force Research Laboratory, claims to have built and tested a working laboratory model. It's a 3-inch copper test rig using a mix of hydrogen and oxygen for fuel, which is the highest-performing rocket fuel for upper stage rocket engines.
"The study presents, for the first time, experimental evidence of a safe and functioning hydrogen and oxygen propellant detonation in a rotating detonation rocket engine," says Kareem Ahmed, an assistant professor in UCF's Department of Mechanical and Aerospace Engineering who led the research. "The detonation is sustained continuously until you cut off the fuel. We have tested up to 200 lbf, but the thrust increases linearly with the propellant mass flow."
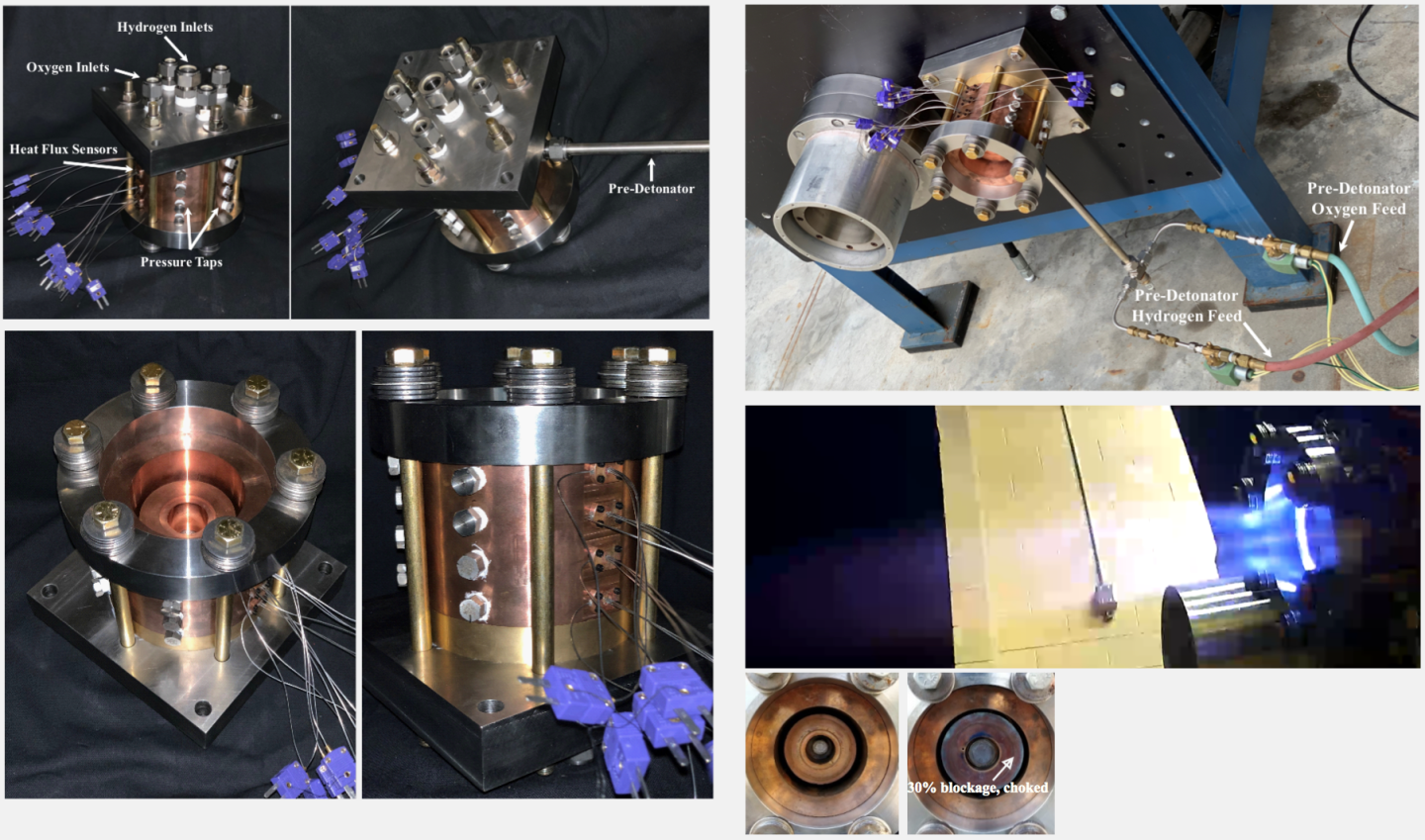
Professor Kareem Ahmed, University of Central Florida
The secret, according to the researchers, was as simple as a tune-up.
"We have to tune the sizes of the jets releasing the propellants to enhance the mixing for a local hydrogen-oxygen mixture," Ahmed says. "So, when the rotating explosion comes by for this fresh mixture, it's still sustained. Because if you have your composition mixture slightly off, it will tend to deflagrate, or burn slowly instead of detonating."
"Just a few months prior, a number of US rocket engine experts had publicly declared that hydrogen-oxygen detonation engines were not possible," Ahmed tells New Atlas. "However, the paper presents experimental evidence and demonstrated without a doubt that detonation of oxygen and hydrogen are occurring within a rotating detonation rocket engine."
"These research results already are having repercussions across the international research community," says William Hargus, lead of the Air Force Research Laboratory's Rotating Detonation Rocket Engine Program, who is a co-author of the study. "Several projects are now re-examining hydrogen detonation combustion within rotating detonation rocket engines because of these results. I am very proud to be associated with this high-quality research."
Ahmed tells us this engine design is being evaluated as a possible replacement for Aerojet Rocketdyne's RL-10 rocket, which was first developed in 1962. Modern versions are still in production for the upper stages of Atlas V and Delta IV rockets, with further versions under development for the Exploration, OmegA and Vulcan rockets, but a proven rotating detonation rocket engine could be a real game-changer.
"The U.S. Air Force is targeting a rocket launch flight test by 2025," says Ahmed, "and we are contributing to achieving that goal."
While space propulsion is the key driver for this research, it also has potential terrestrial uses in other cases where high power and low fuel consumption could make a big difference. In 2012, the Naval Research Laboratory estimated that rotating detonation engines could save the Navy 15-20 percent off a ~US$2-billion annual fuel bill if they were retrofitted in place of the gas turbine engines that run over 100 of its large ships. They could also potentially be used in hypersonic and supersonic flights, or even electric power generation, and Ahmed tells us the design has potential as a booster stage engine as well, but it'd require a different type of propellant.
See a short slow-motion video of the rocket firing below.
Rotating Detonation Engine
The team has published their results in the journal Combustion and Flame.
Source: University of Central Florida