![]() |
1. Environmental Context:
- - Transportation accounts for 29% of US greenhouse gas emissions
- - California mandated all new cars must be zero-emissions vehicles by 2035
- - EVs are seen as crucial for reducing climate change impacts
- - EV batteries use lithium-ion technology similar to phones/laptops
- - Key materials include lithium, nickel, cobalt, manganese, and graphite
- - Materials are currently sourced globally, with significant deposits discovered in California's Salton Sea
- - US lacks domestic capability for full battery production
- - Significant investment needed in infrastructure and workforce training
- - Even when powered by non-renewable electricity, EVs still provide environmental benefits over gas vehicles
- - Batteries typically last 10+ years
- - Secondary uses are possible but face economic challenges
- - Recycling is technically possible but currently complex and expensive
- - New recycling technologies and companies are emerging
- - Balancing environmental protection with industrial development
- - Building necessary infrastructure while managing environmental impact
- - Requires coordination across society, including researchers, engineers, and policymakers
Additional Considerations
What the article covers:
1. Material Sourcing Environmental Impact:
- - Only briefly mentions mining is "extremely efficient" without discussing environmental costs
- - Notes the Salton Sea lithium extraction might face challenges with heavy metal contamination
- - Does not discuss the environmental impact of mining cobalt, nickel, or other materials
2. Manufacturing Environmental Costs:
- - The article is notably light on discussing manufacturing environmental impacts
- - Does not address energy consumption in battery production
- - No discussion of water usage or pollution from manufacturing processes
- - Current recycling requires high-temperature furnaces to burn away materials
- - Process uses strong acids and harsh chemicals for metal extraction
- - Ceramic components often end up as road material or waste
- - Notes recycling is "technically possible" but economically challenging
- - No detailed discussion of environmental impacts from recycling processes
- - The article does not address the infrastructure impact of heavier EVs at all
- - No mention of road wear and tear
- - No discussion of increased energy requirements due to weight
These are significant gaps in the article's analysis. A more complete discussion would need to include:
- - Full lifecycle environmental assessment of battery production
- - Quantitative data on mining impacts
- - Infrastructure costs from heavier vehicles
- - Comparative analysis of environmental costs between battery and conventional vehicles
- - Specific environmental impacts of recycling processes
Electric Vehicle Battery Analysis: Environmental, Safety, and Infrastructure Impacts
1. Environmental Impact & Manufacturing
Material Sourcing
- IEA "The Role of Critical Minerals in Clean Energy Transitions" (2021)
https://www.iea.org/reports/the-role-of-critical-minerals-in-clean-energy-transitions
- Details environmental impact of cobalt mining in DRC
- Water consumption in lithium extraction
- Land use changes from mining operations
Manufacturing Environmental Costs
- Nature Energy: "Comparative life cycle assessment of lithium-ion batteries with different cathode chemistries"
https://doi.org/10.1038/s41560-020-00731-3
- CO2 emissions during production
- Energy intensity of cell manufacturing
- Water consumption metrics
Lifecycle Analysis
- Union of Concerned Scientists: "Driving Cleaner: Electric Cars and the Environment"
https://www.ucsusa.org/resources/driving-cleaner
- Complete lifecycle emissions comparison
- Regional variations in environmental impact
- Grid energy mix considerations
2. Infrastructure Impact
Road Wear
- Transportation Research Board: "Pavement Impacts of Autonomous Electric Vehicles" (2019)
https://www.nap.edu/catalog/25381/
- Additional road maintenance costs from increased vehicle weight
- Impact on bridge infrastructure
- Acceleration of pavement deterioration
Grid Infrastructure
- DOE Grid Integration Tech Team: "A National Blueprint for Lithium Batteries"
https://www.energy.gov/eere/vehicles/battery-500
- Power grid upgrade requirements
- Charging infrastructure needs
- Peak load management strategies
3. Safety Concerns
Fire Risks
- NFPA Electric Vehicle Emergency Field Guide
https://www.nfpa.org/ev-emergency-field-guide
- Thermal runaway characteristics
- Firefighting protocols for EV fires
- Reignition risks
Crash Safety
- IIHS Status Report: "Electric vehicles' weight raises injury risks"
https://www.iihs.org/news/
- Impact of mass on collision outcomes
- Comparison with conventional vehicles
- Structural design considerations
Vehicle Dynamics
- SAE Technical Paper 2020-01-0939: "Analysis of Electric Vehicle Handling Characteristics"
- Brake fade analysis
- Weight distribution effects
- Tire wear patterns
4. Specific Safety Challenges
Battery Thermal Management
- Journal of Power Sources: "Thermal runaway prevention in lithium-ion batteries"
https://doi.org/10.1016/j.jpowsour.2019.227005
- Temperature monitoring systems
- Cooling system requirements
- Failure mode analysis
Emergency Response
- National Transportation Safety Board Safety Report: "Electric Vehicle Fires"
https://www.ntsb.gov/safety/Pages/default.aspx
- First responder protocols
- Specialized equipment needs
- Training requirements
5. Key Statistics (Pre-2024)
- Average EV battery weight: 400-800 kg
- Typical range impact from weight: 10-15% reduction per 100 kg
- Fire incident rate comparison: [Note: Statistics should be updated with current data]
- Average lifetime CO2 emissions comparison: [Note: Varies by region and grid mix]
Research Centers & Resources
- Argonne National Laboratory
- ReCell Center: Battery recycling research
- GREET Model: Lifecycle analysis tools
- Oak Ridge National Laboratory
- Vehicle Systems Integration Laboratory
- Power Electronics and Electric Machinery Research
- National Renewable Energy Laboratory (NREL)
- Transportation and Hydrogen Systems Center
- Battery Thermal Testing Laboratory
Notes on Data Currency
- Safety statistics should be regularly updated
- Environmental impact assessments vary by region and manufacturing location
- Grid energy mix continues to evolve, affecting lifecycle calculations
- Technology improvements may affect weight and safety characteristics
UC San Diego experts weigh in on each stage of a typical EV battery’s life cycle and share their thoughts on what the future might hold.
This article originally appeared in the fall 2024 issue of UC San Diego Magazine as “The Battery (EV)olution” with the sidebar "Are You Ready to Make the Swap?" and the companion article "Charging Ahead."
A fully electric vehicle fleet is globally hailed as a transformative solution to slow climate change. But how green are EV batteries? Will they help save us from a warming planet or add to an ever-increasing problem?
Within the U.S. alone, the transportation sector was responsible for 29% of all greenhouse gas emissions in 2022, more than any other sector. And according to the U.S. Environmental Protection Agency, nearly 80% of these emissions come from vehicles that travel on the nation’s roads and highways.
“A future where the transportation sector transitions to EVs would be a game changer,” says Patricia Hidalgo-Gonzalez, an assistant professor in the Department of Mechanical and Aerospace Engineering at the Jacobs School of Engineering and affiliate member at the UC San Diego Center for Energy Research. “Greenhouse gas emissions have caused global temperatures to increase, which already has caused very serious environmental impacts, such as acidification and warming of the ocean, melting of glaciers and extreme weather events.” She adds, “It is of utmost importance that we put our best efforts to mitigate climate change and prevent it from having more frequent and adverse impacts.”
To help lessen the global warming caused by these emissions, in 2022, the California Air Resources Board approved a nation-leading clean car rule that drew a year-by-year roadmap, with all new cars and light trucks sold in California required to be zero-emissions vehicles by 2035. The mandate allows car manufacturers to make up their car sales in the state with 20% of plug-in hybrid vehicles — which combine gas and electricity — with the remainder of their sales to comprise full-battery electric and hydrogen fuel cell vehicles. With this charge, California joined several other countries in its efforts; other states, including Oregon, Massachusetts, Washington and New York, are following its lead.
Early adopters have paved the way, and sales of EVs continue to climb worldwide. EVs have become more economical and attractive than ever before, with more car companies offering hybrid or full-battery electric vehicles. The battery is what makes an EV possible, typically a lithium-ion battery. And much like traditional, fossil fuel-powered internal combustion engines, these batteries are made from limited natural resources.
Battery Basics
Surprisingly, the cells used for EV lithium-ion batteries are not terribly different in components from cell phone and laptop batteries, explains Ping Liu, professor and the William Coles Endowed Chair in the Aiiso Yufeng Li Family Department of Chemical and Nano Engineering at the Jacobs School of Engineering, and the director of its Sustainable Power and Energy Center.
The battery cells are “the heart of a battery,” Liu says and the number of cells in a battery dictates both its size and capacity.
There are four main components that comprise each battery cell: the cathode, the anode, the electrolyte and the separator. The parts can be thought of as a sandwich, with the cathode and anode serving a similar role to the outer bread slices, while the electrolyte and separator are like the fillings. Multiple elements are typically used within these cells, including lithium, nickel, cobalt, manganese, iron, graphite and copper, among others.
Sourcing the various materials needed for lithium-ion batteries involves countries from across the globe. Much of the world’s supply of lithium is located in Bolivia, Chile and Argentina; the cobalt primarily comes from the Democratic Republic of the Congo; phosphates from countries in Africa; graphite from northern China; and nickel from Australia, Indonesia, Canada, Brazil and Russia. Manganese and iron can be sourced from many places. Most of these metals are mined.
“Mining these days is extremely efficient,” says Liu. “But, at least for lithium, mining is not the only way to source the metal.”
The U.S. is poised to become a lithium powerhouse. A 2023 study by the Lawrence Berkeley National Laboratory revealed a staggering amount of lithium — 3,400 kilotons — within geothermal brines beneath Southern California’s Salton Sea. The geothermal brines — hot, concentrated saline solutions that can be used to generate power — could potentially supply enough lithium for over 375 million EV batteries, far surpassing the total number of vehicles currently on U.S. roads.
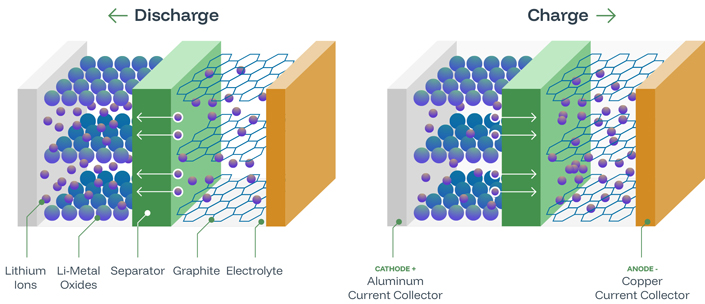
Lithium-Ion Battery: There are four main components that comprise each battery cell: the cathode, the anode, the electrolyte and the separator. These elements perform differently depending on whether the battery is charging or discharging energy.
Construction of the first dedicated, large-scale lithium extraction and renewable geothermal facility in the Salton Sea area began in 2024.
Yet Liu offers a caveat: “The Salton Sea has a lot of other heavy metals in it, and getting lithium out versus getting out lithium that’s useful are two completely different things,” he says. “Extracting something that’s pure enough, free of contaminants, suitable for battery use and for it to make economic sense — those are different questions altogether.”
Mass Production
Domestically, the U.S. currently does not have a way to source all the raw materials for lithium-ion batteries or any commercial manufacturing plants to build the batteries at scale. To do so would involve significant capital investment in physical public infrastructure as well as in training a workforce and building out the necessary facilities.
“The U.S. has a long road ahead as it explores a move toward EV battery manufacturing,” says Liu.
Initial thoughts were that the U.S. could develop battery manufacturing facilities in Imperial County to use the lithium as close to its extraction point as possible. But there are additional energy, water and transportation infrastructure — as well as workforce training — hurdles that have to be overcome before those facilities can be built, explains Isaac Martin, a professor and the chair of the Department of Urban Studies and Planning in the School of Social Sciences. Martin is studying the ability for high-wage, high-skilled blue collar labor to be expanded in the area as a result of the lithium discovery.
Daily Driver
4 Once the raw materials for the batteries are sourced, they are manufactured and installed. Most EV batteries will last at least 10 years.
Yet, one of the widespread criticisms of EVs is that they use electricity that might not be generated by renewable resources. So isn’t using an EV run by, for example, coal-powered electricity just as bad for the environment?
That is not the case at all, answers Liu.
Even if EVs are charged with electricity that is generated by a problematic source, they still offer an environmental benefit.
“Gasoline vehicles are a problem,” says Liu. “Not only are they polluting, they are also polluting in a diffuse fashion because there are so many vehicles dispersing their pollutants as they travel.” A power plant that might be emitting greenhouse gas and pollution, however, is doing so in a concentrated fashion that is likely located in more remote areas, so environmental mitigation and cleanup are easier to manage.
“The Salton Sea has a lot of other heavy metals in it, and getting lithium out versus getting out lithium that’s useful are two completely different things.”
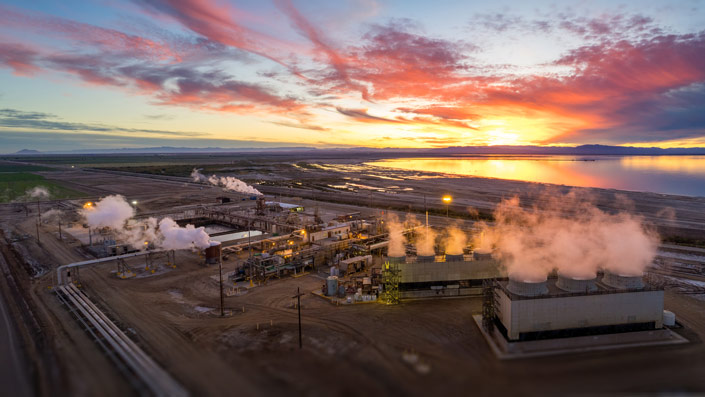
Industrial geothermal plants located near the Salton Sea generate power from the hot, concentrated saline solutions located deep underground. (Photo by iStock)
“People who don’t like EVs usually say that if the electricity is dirty, you actually do not save anything,” says Liu. “But that’s not really true — there is still a benefit as well as a potential to utilize clean energy to power them.”
Beyond their eco-friendly advantages, EVs are better equipped to handle the growing computing power needed to operate today’s advanced cars. While gasoline-powered vehicles have alternators that can create the electrical energy needed to operate onboard computers, Liu explains, EVs can easily run the existing computer systems with the capability to operate even more complicated ones as designs evolve. “As you need more and more electric-powered elements in vehicles, particularly in fully autonomous vehicles, electrification is made for it,” says Liu.
Reuse and Recycle
Just because an EV might reach the end of its primary use doesn’t mean its battery is dead. According to Liu, after years of easy use, such as short daily commutes, these batteries could have a second life. However, the reuse of EV batteries comes down to economic feasibility. “There are a lot of intuitively good ideas that turn out to be quite costly,” says Liu. Finding a secondary use for an EV battery “sounds like a great idea because the battery isn’t dead, so we should squeeze more out of it,” he says. But “after the battery has serviced the car for, say, eight years, and you take it out, then you have to recertify the battery,” he adds. “It is still good, but is it still safe? You may need to separate the good cells from the bad ones before putting the battery back together.”
But once the EV battery has officially reached the end of its life, what’s next? Well, recycling doesn’t quite look like what you’d expect, but it is possible.
“When these batteries were originally designed, they were not designed to be recycled,” says Liu. “In fact, the lithium-ion battery is probably one of the most difficult batteries to recycle.”
So while recycling is possible, Liu says, the issue is at what economic and environmental cost.
Today, lithium-ion batteries are recycled by refinery companies such as Umicore, a large-scale battery recycling company headquartered in Belgium that has been operating for decades. “Traditional recycling involves burning the existing batteries in a high-temperature furnace,” explains Zheng Chen, a professor in the Aiiso Yufeng Li Family Department of Chemical and Nano Engineering at the Jacobs School of Engineering.
“Graphite and other organic materials will be burned away, and the rest of the materials will fuse together to form two components: a metal alloy and ceramics,” says Chen. “The ceramics have minimal value and are often dumped or repurposed to pave the roads.” The metal alloy, on the other hand, contains valuable elements. However, extracting these elements requires further treatment with strong acids and other harsh chemicals to separate and purify the metals. “These metals will be reused for making precursors that can be further processed to make new battery materials,” he adds.
Despite the cost of recycling, Liu is confident that as EV batteries reach the end of their lifespan, they will never cause an e-waste crisis. “Everything can be recycled,” he says.
And Chen is positive about the future. The U.S. Department of Energy and the California Energy Commission are very interested in expanding the domestic capability of EV battery recycling, and the number of startups in this space is growing. Chen himself is part of a startup, ExPost Technology, that is focused on a new recycling strategy for lithium-ion batteries.
The Potential of Change
When it comes down to it, will EV batteries make a difference? And will the U.S. and California be able to make the necessary regulatory changes and infrastructure investments to build up battery manufacturing plants and recycling?
“The overall benefits of EVs are that they’re a way to radically reduce our dependence on fossil fuels and, in particular, to lower emissions,” says David Victor, a professor and the Peter Cowhey Center on Global Transformation Chair in Innovation and Public Policy at the School of Global Policy and Strategy and the director of the Deep Decarbonization Initiative.
Yet with any technological change comes questions of feasibility. “One of the challenges in the clean energy revolution is how do you manage priorities when they conflict — how do you keep those conflicts from generating paralysis?” says Victor. “The U.S. and California are aggressive about environmental protection but make it really hard to build anything that disturbs the environment.”
Victor adds, “What we do know about the clean energy revolution is that we’re going to have to build stuff,” such as industrial facilities, power lines and mines.
And Liu is quick to point out that there is a lot of innovation currently going on. “It will require a lot of ingenuity from all the students and researchers, engineers and policymakers, and everyone to make it happen.
“To stand up an industry will take the whole society,” Liu says. “It will be very difficult. But it can be done.”
Read more about UC San Diego researchers work in "UC San Diego Researchers at the Forefront of the EV Battery Revolution."
One of the challenges in the clean energy revolution is how do you manage priorities when they conflict — how do you keep those conflicts from generating paralysis?
No comments:
Post a Comment